NiTech Solutions x Croda Europe
Integrating flexible manufacturing techniques into the production of everyday products
The challenge
The chemical manufacturing industry plays a significant role in the UK economy. Specialty chemicals are critical to the performance of a wide range of household products including personal care, paints and coatings, adhesives and medicines.
Today’s cost of living crisis means that cost and performance have become even more important for profitability, particularly as environmental and Net Zero pressures mount. As a result, leading companies are increasingly focusing on advanced manufacturing technologies to help them reduce waste and increase efficiency.
These drivers were the basis for a ground-breaking project involving Croda, a leading global manufacturer of life science and consumer care products, technology supplier NiTech Solutions, with support from CPI and the University of Cambridge’s Institute for Manufacturing (IfM). The aim was to allow Croda to replace traditional batch-process technology in a core product area with NiTech’s safer, greener, faster, and cheaper patented continuous oscillating baffle reactor (COBR) technology.

““The aim of the Innovate-funded project was to capture the benefits of NiTech’s COBR technology. Croda, NiTech and CPI worked together to develop the necessary process at lab and then pilot scale, and then successfully implemented it on Croda’s site at industrial scale, with IfM also helping to identify the business model changes required to make this process change possible. Now we have novel UK-developed technology deployed in the industry to manufacture everyday products more efficiently.””
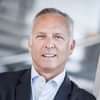
How CPI helped
- Providing access to state-of-the-art facilities for scaling up the technology for the commercial market.
- Assisting with convening the appropriate parties to form the project team and then submitting a successful Innovate UK grant application.
- Focussed the Croda team to deliver key data required for scale-up including the reaction kinetics, which gave significant insight into the optimum process window not only for conversion to a continuous process but also the existing batch process.
- Utilising its skills in operating the NiTech-supplied COBR reactor with the hazardous raw materials required by Croda to demonstrate the feasibility of converting the process to continuous operation.
- Working with the partners to provide valuable reaction data from this demonstration to allow Croda and NiTech to design and supply a pilot reactor for operation on Croda’s site, which ultimately provided the data and confidence Croda needed to proceed with a commercial plant.

Achievements
- Demonstrated that integrating COBR technology achieves process sustainability, efficiency and flexibility improvements with more consistent product quality.
- Increased Croda’s functional molecule and surfactant production capacity by more than 50% without needing more space for their production facility.
- Bridged the gap to turn a lab-functional equipment into a market-ready technology.
Impact
We enabled NiTech Solutions to scale up its innovative flexible manufacturing technology in a new application, allowing it to be deployed into industrial use by Croda. In addition, the University of Cambridge’s Institute for Manufacturing joined the consortium to provide expertise in analysing the business model for the full-scale commercial adoption of these flexible manufacturing techniques.
A successful and competitive chemicals industry must be flexible and adaptable. By working effectively together, the project team enabled the integration of novel manufacturing technology within existing manufacturing facilities, thereby helping Croda to realise a significant capacity increase without impacting product quality or needing significant infrastructure investment. This success helps position the UK as a global leader in next-generation processes and ensures it remains a competitive place for manufacturing.
Compared with traditional batch production, continuous manufacturing approaches like COBR are much better news for the planet. They use less energy – leading to reduced greenhouse gas emissions – and run more efficiently thanks to improved chemical conversion, and heat and mass transfer. Better yields and reduced production of byproducts also reduce how much raw materials are needed. We expect to unlock more sustainability benefits as the technology is developed and adopted.
We are now further working with NiTech and other industrial partners to scale up continuous flow-chemistry manufacturing processes to many other products, such as batteries and nanoparticles. This breadth of capability will help boost UK innovation across the chemicals sector.
Partners
Related
Technologies
Markets
