The drive to better battery technology
Discover how the growth of the battery industry in the UK is powering the future of electric vehicles.
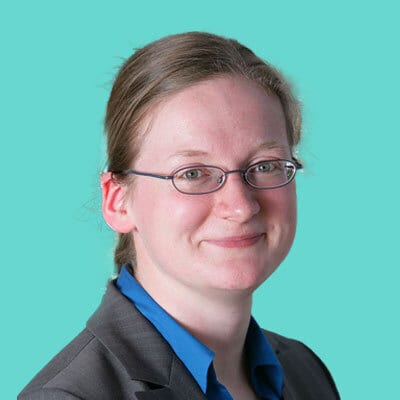
Chief Technologist
The electrification of transport is one of the major trends of the 21st century, and one of the biggest challenges taking on a zero-emission energy approach. Although climate change and air quality began the revolution, the economic benefits of electric vehicles have accelerated interest in cheaper and higher-performing machines.
In the past few years alone, global sales of electric cars have dramatically increased, from 2.1 million in 2019 to an estimated 3.1 million electric cars sold in 2020 with car manufacturers proudly showcasing ‘Going Electric’ slogans with the release of more efficient, purely electric vehicles.
Beyond personal use, the push towards an electrification age has continued with the launch of inter-city shuttles using electric-powered buses and even electric commercial aircraft looking to transform the aviation industry. With more than 30,000 charging stations already installed in the UK, there are already more places to charge an electric car than to fill up a fuel tank. And this number will only increase with the government investing £1.3 billion in electric vehicle infrastructure across the UK. The question is not if, but how far electrification of transport will go – and the answer relies heavily on a single factor: battery technology.
Growth of the battery industry in the UK
Electric vehicles use battery systems to provide power, thereby reducing and ultimately eliminating the need for liquid fuels in-vehicle operation. These batteries will need to be charged using electricity from the national grid, which could lead towards an ultimate zero emission energy source – given that the traditional natural gas energy used to power the grid is being increasingly replaced by greener solutions such as solar, wind, and hydropower energy generation.
Development of improved battery technology and manufacturing is underway within the UK, with the Government releasing industrial strategies and backing Grand Challenge funds to address this critical mission. Most recently they announced an ambitious ‘Ten Point Plan’, which includes; ‘From 2030, ending the sale of new petrol and diesel cars and vans, with all vehicles being required to have significant zero-emissions capability (e.g. plug-in and full hybrids) and be 100% zero emissions from 2035.’



To support this change there will be encouragement for consumer uptake using tax incentives. Alongside this, there is still a significant need to support the UK battery industry to develop the supply chain to meet this increase in demand.
Global battery cell production largely takes place in Asia with 90% manufactured in either China, Japan, or Korea. To meet consumer demand and many countries’ government emissions targets, global production needs to increase up to four times. Europe is the fastest growing market for electric vehicles and many European countries are announcing investment in ‘gigafactories’ for battery cell production to localise the supply chain for automotive manufacturers. The UK currently has one active gigafactory (Envision AESC in Sunderland) and two planned gigafactories; Britishvolt in Blyth and AMTE Power (location yet to be confirmed).
To support these production facilities, there is also a drive to localise the materials supply chains within the UK. This is a strong focus of both the Faraday Battery Challenge (Industrial Strategy Challenge Fund) and the Advanced Propulsion Centre (APC), alongside developing next-generation batteries with improved performance, safety and cost. Together, the total funding available across the value chain from these funding competitions is approximately £1.3 billion.
Various technical challenges have been identified as key to the growth of the EV market. These are related to both manufacture of the cells and the consumer requirements. The APC has identified numerous opportunities for UK suppliers to develop the supply chain required to support this growth, including several related to materials that could be worth up to £12 billion.
This is reflective of the fact that cell materials account for over half of the overall cost of a typical lithium-ion battery (LIB) used in an EV battery pack. The cathode material can be as much as 40% of the overall cost of the cell materials and as such much current research and development focuses on innovations around the production, chemistry and performance of this material set as this could have a large impact on the techno economics of EV cells.
Typical materials used in LIB production include lithium, cobalt, nickel, manganese, and graphite, materials that will be in high demand as battery production increases. In particular, the supply of cobalt poses great concern with both ethical and environmental unease around their extraction from artisanal mines using child labour in the Democratic Republic of Congo.
Lithium mining in addition is a very inefficient process, for example, it can take 750 tons of brine to produce 1 ton of lithium, which has caused controversy in Chile due to the environmental impact of excessive use of water in the process. Therefore, establishing a route to efficient recycling of batteries, where as much as 50% of the materials used can be recycled, should lead to a more sustainable supply chain. Several options exist to recycle LIBs including pyrometallurgical and hydrometallurgical.

Technical challenges in the battery industry
However, the complexities of the battery packs used in EVs, the variety of chemistries used within these cells and the inefficiencies in the recovery of the critical materials mean that there are still many challenges to be overcome in this area.
The use of more sustainable materials sets in the LIBs is one area of interest currently and using ‘recycling by design’ to enable a more circular economy around the EV battery market. Re-use of these battery packs in another application may be a further viable option, with initiatives existing that take used EV batteries and apply them in stationary storage applications. To enable this, advanced sensors and improved methods for monitoring the characteristics of the LIBs at end-of-life would be beneficial.
Finally, the performance of the battery cell for use in EV applications is paramount. Consumer appetite is for an electric car that can match the ease of fuel re-fill and range of a petrol or diesel car. The rate of charge and range is related to the power and energy density of the LIB.
Current EV models do now meet the typical range requirements for daily use within excess of 250 miles on a single charge common across multiple EV models and manufacturers. This demonstrates that the energy of the battery packs within these models can be engineered to meet consumer demand. The reality is that this requires a very large number of cells to be used in each EV.
For example, a Tesla Model S contains over 7,000 LIB cells weighing 540 kg. Significant efficiency and cost gains could be achieved if the energy density of each individual LIB cell could be improved. The rate of charge remains slower when compared to a petrol or diesel car fuel tank re-fill, with times typically many hours for a full battery charge. Commonly EV users would therefore plugin and charge whenever there is an opportunity rather than wait for a flat battery.
Improvements in infrastructure, engineering, and LIB cell chemistry could lead to improvements by allowing a higher current rate to be accepted and therefore reducing the time of charge. As can be seen, battery innovation needs to achieve a lower purchase price, more efficient charging, larger capacity, extended lifetime, and, of course, greater safety. These challenges can in part be addressed by innovations in materials, manufacturing and cell technologies.

Battery development at CPI from materials and formulation to application
CPI’s core expertise in product and process development acceleration is highly relevant to battery materials optimisation and cell manufacturing, demonstrated by our extensive project portfolio in the area representing a wide variety of chemistries, printing processes and cell technologies. CPI has a portfolio of work across the technology readiness levels, within which the materials area focuses on production and scale-up of active materials.
Formulation describes the optimisation of components within electrode coatings primarily, whether they are known or novel materials. The coatings area encompasses the deposition of these formulations via a wide variety of techniques, from solution to vacuum deposition. Finally, the application area describes anything from coin cell testing as a means for materials screening to the development of smart cell monitoring.
The materials activities largely utilise our process engineering and chemistry expertise with support given to collaborators in scaling-up their materials in the most efficient and economic manner. This can be via technoeconomic analysis (TEA), life-cycle analysis (LCA) or a lab-based process development project looking at optimising synthesis steps.
Funded by the Faraday Battery Challenge, UK-NVBCSC saw CPI develop a lab process for producing anode material and supporting the development of a UK based supply chain to enable cell manufacturer AMTE Power to supply niche vehicle partners, Delta Motorsports and Williams Advanced Engineering, with high performance battery cells. The large number of formulation and coating projects within the portfolio demonstrate the existing expertise within CPI and the challenge that materials and technology developers are facing in developing their products and processes. CPI is applying industry knowledge and capabilities from sectors such as paints, electronics and FMCG to support these projects.
CPI is chemistry and technology agnostic and hence work with both cathode and anode materials, Li-ion and Na-ion, as well as liquid and solid-state electrolytes. Printing processes utilised within these projects range from the liquid processing such as the industry standard slot-die to screen printing, 3D printing, and for vacuum deposition techniques such as ALD, PVD and thermal evaporation. These projects utilise the range of scales that can be undertaken at CPI from benchtop process development to scale-up demonstration at R2R. Utilising both our formulation and coatings expertise, PowerDrive Line is a £4.4m project developing a proof of concept prepilot line for production of solid-state batteries and is a collaboration with the only UK manufacturer of solid-state Li-ion batteries, Ilika. CPI has successfully developed stable and printable formulations for several layers in the solid-state battery stack, with Ilika utilising scaled up inks within their production process to produce up to 250 cells per week.
Finally, the projects within the application area are largely related to application of our sensor capabilities, developed over the last 15 years within the field of printed electronics. With our collaborators, CPI are developing the integration of sensor technologies into battery cells to measure changes such as pressure and temperature. Albatross is an EU funded project between 10 countries and 21 partners.
CPI will be working closely with project partner PST to develop and integrate sensing technology as part of the battery management system (BMS) to provide a lightweight, cost effective solution to battery lifetime monitoring. CPI has further capability to integrate electronics on a reel, combining sensors, circuitry, processing, energy, and communications – creating new form factors for electronics for battery management systems.

CPI supporting a global change in battery development
With global governmental policies driving the net-zero agenda and a strong consumer demand forecast for electric vehicles to meet these regulations, there is clearly a need to support the development of battery cell chemistries and technologies, both within the UK, Europe and further afield. CPI has energy storage technologies firmly within its strategic goals and will be continuing to support companies in overcoming their challenges related to materials, formulations, coating and sensors.
Discover how we support companies in their battery materials innovation.
Enjoyed this article? Keep reading more expert insights...
CPI ensures that great inventions gets the best opportunity to become a successfully marketed product or process. We provide industry-relevant expertise and assets, supporting proof of concept and scale up services for the development of your innovative products and processes.