The 21st century materials and energy powering the future of farming
The 21st century materials and energy powering the future of farming
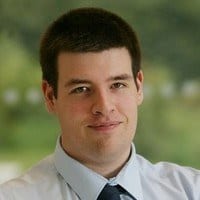
Technology and Innovation Officer
Farming has undergone huge changes in the last few centuries. From pre-industrial revolution when much of society worked 6 days per-week during daylight hours to grow food to feed the country.
The Agricultural Revolution in the mid-18th century, realised through inventions and innovations such as the seed drill invented by Jethro Tull, enabled significant gains in productivity that then created the conditions that enabled the Industrial Revolution to happen because the reduced workload on the farms meant that people were able to move from the countryside to the growing cities. The pace of change in agriculture has not significantly slowed, now not only the mechanisation of the planting and harvesting of food but the scale of automation of these activities in the UK is massive; 75% of our land area is worked by around 364,000 people, only 1.1% of the UK’s working-age population.
Reports by Defra show that the energy usage per hectare of land varies significantly with different types of farm: grazing livestock farms 1.5 to 3.6 GJ per hectare, while dairy farms use 13.4 GJ due to significant use of milking machines. Raising pigs uses 17.3 GJ per hectare, while chickens use by far the most energy at 45.8 GJ per hectare due to the energy intensive chicken sheds.
Arable crops (cereals) need far less energy than intensive animal farming at only 7.4 GJ per hectare, although they still use more energy than grazing livestock. The increase in energy used to grow cereals over grazing is due to the energy needed to run farm machinery for ploughing, planting and harvesting. This is generally consumed in the form of red diesel, which is essentially the same fuel as used for road vehicles but has a rebate that lowers the tax from 58p per litre to 11 pence per litre.
In the UK in 2019, the harvest of wheat was 16.3 million tonnes, an increase of 20.1% over the previous year. This gives a productivity of 9.0 tonnes per hectare, and gives a 5‑year average of 8.3 tonnes per hectare. The majority of the energy to grow this (67%) comes in the form of red diesel at 106.9 litres per hectare per year, and electricity making up the second biggest energy source at 18%, at 115 kWh/year. The remainder is made up of road-fuel, kerosene and liquified petroleum gas.
Substituting red diesel for non-fossil fuels is not going to be easy; biodiesel is an obvious source, however most sources of first-generation biofuels are food crops, such as sugar cane, maize, palm oil, and soybean, and second-generation fuels from biomass-waste are still being developed at 100 – 200 litres of fuel per dry tonne. Therefore, either a significant area will need to be given over to growing fuel to grow food, or the maximum energy will need to be harvested from the non-food growing areas such as solar cells on building roofs, as light-weight structures covering farm yards and arrays in otherwise non-productive fields that are difficult to grow on.
Michael Eavis, owner of Worthy Farm that hosts the Glastonbury festival has one of the largest privately owned PV arrays in the country; 1,300 panels on the roofs of the dairy sheds generating over 250,000 kWh of electricity per year. Wind turbines will play a significant role where appropriate. Potentially nuclear-powered tractors could be tilling the fields, but that is a long way in the future.

FabriGen
To reduce the amount of power coming from fossil fuels, CPI worked with a consortium of UK and European companies in the FabriGen project to develop photovoltaic cells for solar canopies that are laminated into large scale tensile membrane structures. The consortium produced organic photovoltaic (OPV) cells of over 6 m long and 50 cm wide on tensile fabrics utilising roll to roll production techniques, 16 m² of active-area material was produced for the final demonstrators. The flexible nature of OPV provides a number of advantages for the solar power industry.
The ability to produce the panels on fabric or plastic surfaces means that complex shapes and structures can be designed to maximise solar collection. In addition, the technology will enable the production of large area panels manufactured in a cost and resource efficient manner, to bring the costs of solar power on par with that of conventional energy.

Solution-processed inorganic thin-film photovoltaic devices (SolPV)
Inorganic materials offer higher conversion efficiency than organic materials but are often associated with higher cost of manufacturing equipment leading to higher cost to produce the final cells. To mitigate this, solution processing of inorganic material is a promising method of getting the best of both worlds, however the structuring of the solution-processed materials is not easy.
Therefore, starting in 2021, CPI is supporting a consortium of three of the UK’s leading academic centres in Cu(In,Ga)(S,Se)2 (CIGS) and Cu2ZnSn(S,Se)4 (CZTS) research to ensure that innovation is not only driven by device design and characterisation but also by scalable manufacturing. The SolPV project aims at taking the performance of solution-processed CIGS and CZTS devices to power conversion efficiencies above 15% using scalable manufacturing routes and Cd-free architectures.
Hydrogen; the fuel of choice of drones
Automation and self-driving vehicles are more advanced in agriculture than any other industry, with mining and construction catching up, and human mobility still many years away. The relatively quiet, predictable and slow moving agricultural vehicles have lent themselves to being made driverless, with GPS and other navigational technologies now a critical part of planting and harvesting machines. The use of drones has increased massively in the USA and Europe to enable farmers to survey their fields efficiently and gain insights on crop health from a vantage point that previously would have been impossible.
The optimal power source for drones to allow higher flight times and increased pay load capacity is compressed hydrogen gas due to its superlative weight-to-energy ratio compared to other fuels and energy storage. However, the generation of hydrogen by the electrolysis of water whose power is generated from renewable sources such as PV is quite poor when the losses from conversion at each stage mount up . Therefore, going straight from sunlight to H2 gas generation via photo electrocatalysis offers a route that could potentially double the available amount of H2 fuel from a solar panel array, although this technology is still in development.
Conclusion
In all likelihood tomorrow’s farmers will get the energy they need to run their machinery and equipment from a diverse range of sources, as they do today, however we can expect that a significant proportion of fossil fuels will be replaced. The diesel, kerosene and LPG coming from fossil fuels will be substituted for bio-diesel or biomass heating from waste sources; renewable electricity from wind and solar arrays in diverse places around the farm where crops are inefficient to grow; and hydrogen fuel from solar arrays to power electrical systems, drones and light vehicles.
Enjoyed this article? Keep reading more expert insights...
CPI ensures that great inventions gets the best opportunity to become a successfully marketed product or process. We provide industry-relevant expertise and assets, supporting proof of concept and scale up services for the development of your innovative products and processes.